Herod’s marine engineers have surprised even their modern counterparts in the ingenuous solutions to the perennial problems of the profession. One of these problems is the seasonal damage caused by waves to the main mole and quays during winter storms. In Caesarea, this problem was solved by building a subsidiary breakwater, called Prokumatia by Josephus. It was about 6m wide and did not rise above water level. It was designed to protect the main mole behind it from the force of the waves and the quays from spray.
A common problem in port engineering is silting, which requires constant dredging, done nowadays with heavy mechanical equipment. Herod’s engineers solved this problem by natural means. In the S/W edge of the middle basin, a channel was carved in the natural rock. It is slightly raised from the sea bottom and goes up to 20-30 cm above sea level. At the sides there are notches for wooden barriers, used to control the flow of water in. East of this point, in the area of the Crusader moat, there were similar channels (these points are not marked, as they are on land). These introduced water into the port, that flowed out through the entrance. This flow continuously flushed out the harbour and prevented silt from coming in through the entrance. A layer of silt about 1m thick was found at the harbour mouth. This layer was full of pottery shards, metal parts and other debris, carried here during the times the port was in use.
The underwater circuit reveals other surprises, such as the sophisticated methods used in building the port. Most of the foundations were made of concrete – a Roman innovation which fell into disuse at the end of the Empire and was rediscovered only in the modern age. The concrete was poured into wooden caissons of varying sizes and forms (14x7m., 15x11m.), prefabricated on shore by master carpenters from the best imported timber. The remains of the caissons are preserved in some areas and in others the impression of the cross beams is visible. The concrete was made of limestone cobbles, lime and an essential quantity of imported volcanic ash (pozzolana), which changed its composition on exposure to water and hardened, much as modern “Portland” cement does in today’s concrete. After pouring some of the concrete into the caissons, they were floated to their designated site and anchored there with iron chains. More concrete was poured in from service boats, until the forms settled on the sea floor. They were then secured in place and the pouring completed to the desired height. The forms were laid side by side serving as artificial islands for the base of the breakwaters. “Caves” or “tunnels” (as the divers call them) discovered at the northern end of the main breakwater, by the harbour’s entrance, proved to be caused by severe erosion of the second phase of construction described above, which contained little or no “pozzolana” additive.
The Roman engineers knew also how to save on costs and materials. Sometimes they used double-walled caissons which they filled with concrete as a frame to an open space. That space was left to fill with sand naturally brought in by the waves.
The loading quays and superstructures were built of huge ashlar blocks, some of them reaching 7m in length and over 10 tons in weight. In places, these huge blocks were joined together by iron clamps, fixed by lead poured in situ.
Written by Sarah Arenson
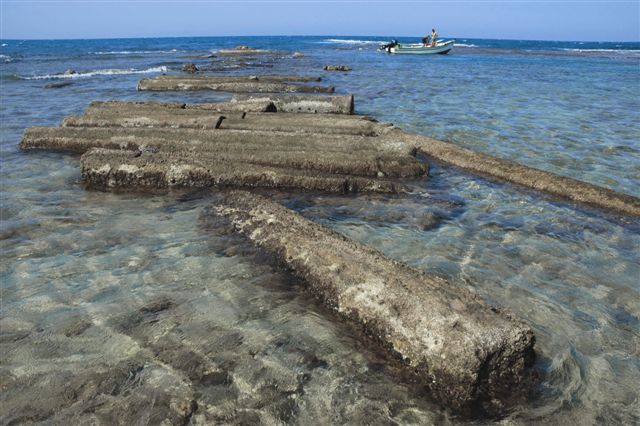